Water for injection or WFI standards as it relates to the International Pharmacological Standards have been brought closer to other nations standards, but there are still significant differences. WFI can be produced with many different treatment processes. These processes meet the United States Pharmacopeia (USP) standards. The Japanese Pharmacopoeia (JP) allows for distillation, reverse osmosis (RO) or ultrafiltration. The European Pharmacopoeia currently only approves of distillation for the sole method of producing WFI.
In the bio-pharmaceutical industry the preferred method for producing WFI has historically been distillation and this is still the case today. However, a lot of other high purity industries utilize RO, deionization and ultrafiltration to produce WFI or even higher quality water in lieu of distillation. Also most industries do not have regulated process limitations. |
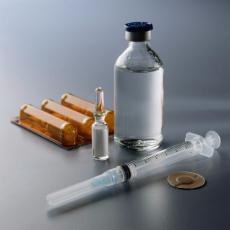 |
The Advantages and Disadvantages of Distillation
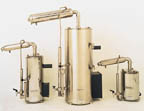 |
In order to meet USP requirements WFI must be produced by using distillation or a purification process proven to be equal to or superior to distillation. The water must pass conductivity tests and total organic carbon (TOC) test, and the bacteria endotoxin levels must be below 0.25 endotoxin units per milliliter (mL). Per 100 mL the microbial level must not be above 10 colony-forming units (cfu). In addition to producing water with low microbial levels, distillation, can also remove endotoxins. |
A vapor compression distillation system typically consists of the following:
- Dual Softeners
- Heat Exchanger
- Hot-Water-Sanitizable Activated Carbon
- 5-Micron Prefilter
- Optional Hot-Water-Sanitizable RO
- Vaopor Compression Still
The advantages of vapor compression distillation:
- Reliable Operation
- Energy Efficient when compared to multiple effect distillation
- Able to be operated on softened/dechlorinated feed
- Does not need nor require a complex system design
- Relatively low maintenance
Stills are reliable but they are not perfect. They can produce pyrogenic product when operated incorrectly or if they have a malfunction. If using high endotoxin feed water when there is membrane based system pretreating the still the water produced from the still may fail the endotoxin test. Vapor compression distillation can also use more energy and have a higher life cycle cost than membrane based systems. They may also require RO r RO/deionization feed as well as requiring more labor than multiple effect stills.
Multiple Effect Distillation Systems (MED) Consists of the following:
-
- Multimedia Filter
- Dual Softeners
- Break Tank
- Heat Exchanger
- Hot-Water-Sanitizable activated carbon
- 5 Micron Prefilter
- Optional pH Adjustment
- 254-Nanometer (nm)UV
- Hot-Water-Sanitizable RO
- Continuous Electrodeionaztion (CEDI)
- Multiple Effect Distillation Unit
In addition to meeting all of the pharmacopeial requirements multi-effect distillation has great advantages including few moving parts which translates into reliable operation.
The disadvantages are as follows:
-
- Requires High Quality Feed Water. Generally less than 10 p.p.m.
- Higher energy costs than with vapor compression distillation
- Can have a higher life cycle cost than membrane systems
- Can fail the endotoxin requirement on high endotoxin feedwater
The advantages to using RO to produce WFI are as follows:
-
- Perhaps the lowest life cycle cost alternative
- Low energy requirements
- Reduces conductivity, TOC, endotoxin, and microbial level
- Reliable operation
- Can be continuously hot santitized
- The USP has some history using RO for WFI
Disadvantages of using RO:
-
- There is limited history as it pertains to using RO for WFI.
- The EP does not allow RO for WFI production
- RO systems require periodic cleaning
- Membranes must be replaced
- Membranes can fail
Other WFI Methods
Endotoxin can be removed by quite a few separation methods such as RO and ultrafiltration (UF). Oxidation with ozone will also remove endotoxins. To achieve low microbial levels in product water, heat, distillation, UF, RO, filtration, ozone, ultraviolet light and chemical methods can be used.
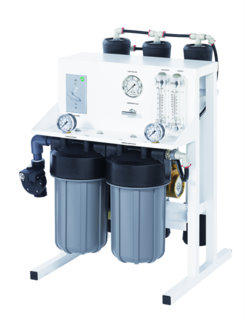 |
One effective way to produce WFI is to use a Two-Pass RO system (TPRO).
A TPRO system consists of the following:
- Multimedia Filter
- Dual Softeners
- Break Tank
- Heat Exchanger
- Hot-Water-Sanitizable activated carbon
- 5 Micron Prefilter
- Optional pH Adjustment
- 254-Nanometer (nm)UV
- Hot-Water-Sanitizable TPRO
Another alternative system could include a hot-water-santitizable RO unit followed by a CEDI unit. Here a continuous hot-water RO unit polishes the water before storage and use as WFI.
|
Ultrafiltration
One common failure with both vapor compression and multiple effect distillation is their failure to treat adequately treat feed water so as to reduce endotoxin levels. According to the U.S. Food and Drug Administration (USFDA) guide for inspections of High-Purity Water Systems states:
"Many of the still fabricators will guarantee a 2.5-log to 3-log reductoin in the endotoxin content. Therefore it is not surprising that in systems where the feed water occasionally spikes to 250 EU/mL, unacceptable levels of endotoxins may occasionally appear in the distillate (WFI). For example three new stills including two multi-effect were found to be periodically yielding WFI with levels greater than 0.25 EU/mL."
They go on to state:
"Pre-treatment systems for the stills included only deionizination systems with no RO, ultrafiltration or distillatoin. Unless a firm has a satisfactory pre-treatment system, it would be extremely difficult for them to demonstrate the that the system is valid."Ultrafiltration is another alternative to distillation and can be conventional UF or continous hot UF. These ultrafiltration modules are available in various materials and configurations. Modules are made with both polymeric and ceramic materials and in spiral wound, hollow fiber, tubular, and multi-channel element configurations. Some modules are designed for ambient temperature operation. Some modules can operate at high temperatures (80oCor higher)continuously or intermittently. Much like distillation units, membrane systems are self sanitizing when operated at continuous high temperatures, like distillation units. To ensure low microbial effluent performance ambient temperature operating systems need to periodically be sanitized.
|
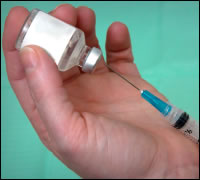 |
A typical ultrafiltration system incorporates the following:
- Hot-water-sanitizable RO
- CEDI
- 10K UF
It should be noted that the second UV and 10K UF after the DECIU can be replaced by a continuous hot UF unit.
The Disadvantages Of Ultrafiltration
- May have the lowest life cycle cost
- Low energy requirements
- Has a significant history of quality WFI water production in the United States and Japan
- Significant U.S. history in active pharmaceutical ingredient (API) production
- Continuous hot operation (80+oC)
- Excellent endotoxin reduction (up to 4 logs)
- Significant pretreatment
- The membrane can fail
- The system requires periodic cleaning
Perhaps the largest disadvantage for UF and WFI production is that it is not allowed by the EP.
In Closing
WFI production has a solid history using the distillation process. In the early years of RO the systems failed to produce quality water. However, today's RO technology can reliably produce WFI as described above. It should be noted that UF-based systems also have a solid history in the production of WFI. In non-regulated industries membrane-based systems have also proven to be viable a producing WFI and high quality waters. Today the EP does not approve of other methods other than distillation. And it seems that this method will not be approved anytime soon. The barrier to membrane-system growth seems to be a greater issue than the technical barriers that are currently present. Membrane technology in Japan and the U.S. has a successful history. It should be pointed out that membrane system implementation is limited to the facilities, applications, where the EP requirements are not a factor.
Remember when deciding which WFI system to implement at your facility consider the following:
- Regulatory compliance
- System reliability in producing WFI quality water
- System capital cost
- Operating Costs
- Maintenance costs
Example of WFI System
A biotech firm had discovered that certain cell cultures did poorly in distilled water and thrived in RO water. The firm wanted to optimize water conservation at the facility so they chose to install a system that consisted of RO, service deionization (SDI)and a second pass RO system. The system is hot-water-sanitizable so as to ensure low microbial counts.
The first-pass RO/SDI system produces USP purified water. A portion of this water then feeds a second single pass RO to produce WFI. The second RO runs at 100% recovery. The entire waste stream is recycled back to the pretreatment break tank. The recovery at the membrane surface is low to reduce the risk of fouling. This also minimizes maintenance and ensures product water quality.
This system produced excellent results. The sell culture process was optimal because the the water exceeded the requirements for WFI. Additionally there were steam savings fo 98% compared to that of a distillation system. The price of the second RO was about half the price of a still. Lastly,the firm was able to save 1.3 million gallons per year in water and sewer charges.
|
|